15-5PH
offers a combination of high strength and hardness, good corrosion resistance plus excellent transverse mechanical properties.CNLHSS Steel 15-5 PH Stainless Steel is the ferrite-free version of CNLHSS 17-4 PH® Stainless Steel. Both alloys are widely used
Product parameters | |
Material category:: | Stainless Steel |
Steel grade:: | 15-5PH |
Place of origin:: | USA |
Description
Mechanical Properties - Physical Properties
Dimensional Change - Corrosion Resistance
More
CNLHSS Steel 15-5 PH® Stainless Steel is a martensitic precipitation hardening stainless steel that provides an outstanding combination of high strength, good corrosion resistance, good mechanical properties at temperatures up to 600 °F (316 °C) and good toughness in both the longitudinal and transverse directions in both base metal and welds.Short-time, low-temperature heat treatments minimize distortion and scaling.This alloy is air melted and AOD refined. For data not available on this alloy,use the CNLHSS Steel 17-4 PH® Stainless Steel sheet data as a guideline when available.
Composition | (wt %) |
---|---|
Carbon(C) | 0.07 max. |
Manganese(Mn) | 1.00 max. |
Phosphorus(P) | 0.040 max. |
Sulfur(S) | 0.030 max. |
Silicon(Si) | 1.00 max. |
Chromium(Cr) | 14.00 -15.50 |
Nickel(Ni) | 3.50 - 5.50 |
Copper(Cu) | 2.50 - 4.50 |
Niobium*(Nb) | 0.15 - 0.45 |
CNLHSS Steel makes no intentional Ta addition.
AVAILABLE FORMS
CNLHSS Steel 15-5 PH Stainless Steel is produced in sheet and strip, in thicknesses from 0.015 – 0.125 in. (0.38 – 3.18 mm). Material is supplied in Condition A, ready for fabrication and subsequent hardening by the user. Since the material transforms to martensite on cooling to room temperature,flatness requirements should be considered and discussed as part of the order.
SPECIFICATIONS
The following specifications are listed without revision indications. Contact ASTM Headquarters for latest ASTM revision.For AMS revision,contact AMS Division of SAE.
AMS 5862
ASTM A693 Plate, Sheet and Strip
(Listed as Grade XM-12 – UNS S15500)
METRIC PRACTICE
The values shown in this bulletin were established in U.S. customary units.The metric equivalents may be approximate.
Standard Heat Treatments
As supplied from the Mill in Condition A, CNLHSS Steel 15-5 PH Stainless Steel can be heat treated at a variety of temperatures to develop a wide range of properties. Eight standard heat treatments have been developed.The following table outlines the times and temperatures required.
This alloy exhibits useful mechanical properties in Condition A. Tests conducted at an exposed marine atmosphere 82 ft. (25 m) from the waterline, show excellent stress corrosion resistance for close to 20 years. Condition A material has been used successfully in numerousapplications. The hardness and tensile properties fall within the range of those for Conditions H 1100 and H 1150.
In critical applications, the alloy is used in the precipitation-hardened condition, rather than Condition A. Heat treating to the hardened condition, especially at the higher end of the temperature range, stress relieves the structure and may provide more reliable resistance to stress corrosion cracking than in Condition A.
TABLE 1 – STANDARD HEAT TREATMENTS
Condition A Solution Treated at 1900 °F ± 25 °F (1038 °C ± 14 °C) or Air cool below 90 °F (32 °C).
Condition | Heat To ± 15 °F (8.4 °C) |
Time at Temperature, hrs. |
Type of Cooling |
---|---|---|---|
H 900 | 900 °F (482 °C) | 1 | Air |
H 925 | 925 °F (496 °C) | 4 | Air |
H 1025 | 1025 °F (551 °C) | 4 | Air |
H 1025 | 1075 °F (580 °C) | 4 | Air |
H 1100 | 1100 °F (593 °C) | 4 | Air |
H 1150 | 1150 °F (621 °C) | 4 | Air |
H 1150 + 1150 | 1150 °F (621 °C) 1150 °F (621 °C) |
4 followed by 4 |
Air Air |
H 1150-M | 1400 °F (760 °C) 1400 °F (760 °C) |
2 followed by 4 |
Air Air |
Forms and Shapes:
Round bar (Diameter): 5.5 mm to 700 mm
Wire rod (Diameter): 0.10 ~ 16mm
Square bar / Flat bar: 5mm to 550mm
Steel strip via cold rolled: T0.1 - 3mm X W5 - 650mm X L (or in coil form)
Forged ring: OD200 ~ 1500mm X ID150 ~ 1250mm X H20 ~ 1250mm
Heavy/middle plate via hot rolled: T50 - 200mm X W80- 1200mm X L1000-3000mm
Forging piece: stepped shafts with flanks / discs /tubes /slugs /donuts /cubes /other different shapes based on OEM.
Length: Fixed length or random length or based on the customer's special requirement.
For all stock availability contact Sales.
CNLHSS Steel 15-5 PH Stainless Steel provides excellent mechanical properties. For applications requiring high strength and hardness plus corrosion resistance, this alloy is an outstanding choice. In addition, it is more cost effective than many high-nickel, non-ferrous alloys.
*Sheets and strip.
TABLE 4 - SHEET CHARPY IMPACT RESISTANCE*
*Average of triplicate tests for two heats.
**Samples were 0.093 in. (2.36 mm) thick with a depth beneath
the notch of 0.314 in. (7.98 mm).
TABLE 5 - MODULUS OF ELASTICITY
Data represent average of two tests from one heat.
The modulus of elasticity of CNLHSS Steel 15-5 PH Stainless Steel at elevated temperatures can be expressed conveniently as % of room temperature modulus. At temperatures ranging from room to 600 °F (315 °C), this material showed the following:
TABLE 6 - EFFECT OF TEMPERATURE ON MODULUS OF ELASTICITY
Poisson’s Ratio in all hardened conditions is 0.272.
*Data represent average of two tests from one heat.
TABLE 7 - PHYSICAL PROPERTIES
For all stock availability contact Sales.
TABLE 2 – TYPICAL MECHANICAL PROPERTIES
Transverse Property | Condition | ||||||
---|---|---|---|---|---|---|---|
A | H 900 | H 925 | H 1025 | H 1075 | H 1150 | H 1150-M | |
UTS, ksi. (MPa) | 160 (1103) | 200 (1379) | 190 (1310) | 170 (1172) | 165 (1138) | 150 (1034) | 137 (945) |
0.2% YS, ksi. (MPa) | 115 (793) | 185 (1275) | 175 (1207) | 165 (1138) | 160 (1103) | 130 (896) | 111 (765) |
Elongation % in 2" (50.8 mm) | 5 | 9 | 9 | 10 | 11 | 12 | 17 |
Rockwell Hardness C | 35 | 45 | 43 | 38 | 37 | 33 | 31 |
TABLE 3 - PROPERTIES ACCEPTABLE FOR MATERIAL SPECIFICATION*
Transverse Property | Condition | ||||||
---|---|---|---|---|---|---|---|
A | H 900 | H 925 | H 1025 | H 1075 | H 1110 | H 1150 | |
UTS, ksi. (MPa) | 185 max.(1276) | 190 min.(1310) | 170 min.(1172) | 155 min.(1069) | 145 min.(1000) | 140 min.(965) | 135 min.(931) |
0.2% YS, ksi. (MPa) | 160 max.(1103) | 170 min.(1172) | 155 min.(1069) | 145 min.(1000) | 125 min.(862) | 115 min.(790) | 105 min.(724) |
Elongation % in 2" (50.8 mm) | 3 min. | 5 min. | 5min. | 5 min. | 5min. | 5min. | 8 min. |
Rockwell Hardness C | 38 max. | 40 - 48 | 38 - 46 | 35 - 43 | 31 - 40 | 31 - 40 | 28 - 38 |
TABLE 4 - SHEET CHARPY IMPACT RESISTANCE*
Condition | Impact Energy, in.•lbs./in.2 (J/cm2)** | |
---|---|---|
Room Temperature | -65 °F (-54 °C) | |
A | 3265 (57.2) | 2669 (46.7) |
H 900 | 2857 (50.0) | 2361 (41.3) |
H 1025 | 3974 (69.6) | 3378 (59.2) |
H 1150 | 4626 (81.0) | 4248 (74.4) |
H 1150-M | 5616 (98.4) | 5049 (88.4) |
Pressed Notch Tests | ||
H 900 | 2184 (38.2) | 1360 (23.8) |
H 1150 | 3406 (59.6) | 2557 (44.8) |
**Samples were 0.093 in. (2.36 mm) thick with a depth beneath
the notch of 0.314 in. (7.98 mm).
TABLE 5 - MODULUS OF ELASTICITY
Condition | ||||
---|---|---|---|---|
H 900 | H 1025 | H 1075 | H 1150 | |
Modulus in Tension, psi. (MPa) | 28.5 x 106 (196 x 103) |
|||
Modulus in Torsion, psi. (MPa) | 11.2 x 106 (77 x 103) |
11.0 x 106 (76 x 103) |
10.0 x 106 (69 x 103) |
10.0 x 106 (69 x 103) |
The modulus of elasticity of CNLHSS Steel 15-5 PH Stainless Steel at elevated temperatures can be expressed conveniently as % of room temperature modulus. At temperatures ranging from room to 600 °F (315 °C), this material showed the following:
TABLE 6 - EFFECT OF TEMPERATURE ON MODULUS OF ELASTICITY
Temperature, °F (°C) |
Modulus of Elasticity*, (% of Room Temperature Modulus) |
---|---|
72(22) | 100.0 |
100(38) | 99.6 |
200(93) | 97.8 |
300 (149) | 96.3 |
400 (204) | 94.7 |
500 (260) | 93.0 |
600 (315) | 91.4 |
*Data represent average of two tests from one heat.
TABLE 7 - PHYSICAL PROPERTIES
Condition | ||||
---|---|---|---|---|
A | H 900 | H 1075 | H 1150 | |
Density, lbs./in.3 (g/cm3) | 0.28 (7.78) | 0.282 (7.80) | 0.283 (7.81) | 0.284 (7.82) |
Electrical Resistivity, µΩ•cm | 98 | 97 | - | - |
Specific Heat,BTU/lbs./°F (kJ/kg/K) 32 – 212 °F (0 – 100 °C) |
0.11(0.46) | 0.10(0.42) | - | - |
Thermal Conductivity,
BTU/hr./ft.2/°F (W/m/K) 300 °F (149 °C)
500 °F (260 °C) 860 °F (460 °C) 900 °F (482 °C) |
- - - - |
124 (17.9) 135 (19.5) 156 (22.5) 157 (22.6) |
- - - - |
- - - - |
Mean Coefficient of Thermal Expansion,
in./in./°F (μm/m/K) -100 – 70 °F (-73 – 21 °C)
70 – 200 °F (21 – 93 °C) 70 – 400 °F (21 – 204 °C) 70 – 600 °F (21 – 316 °C) 70 – 800 °F (21 – 427 °C) 70 – 900 °F (21 – 482 °C) |
- 6.0 x 10-6 (10.8) 6.0 x 10-6 (10.8) 6.2 x 10-6 (11.2) 6.3 x 10-6 (11.3) - |
5.8 x 10-6 (10.4) 6.0 x 10-6 (10.8) 6.0 x 10-6 (10.8) 6.3 x 10-6 (11.3) 6.5 x 10-6 (11.7) - |
- 6.5 x 10-6 (11.7) 6.5 x 10-6 (11.7) 6.6 x 10-6 (11.9) 6.8 x 10-6 (12.2) - |
6.1 x 10-6 (11.0) 6.6 x 10-6 (11.9) 6.9 x 10-6 (12.4) 7.1 x 10-6 (12.8) 7.2 x 10-6 (13.0) 7.3 x 10-6 (13.1) |
For all stock availability contact Sales.
DIMENSIONAL CHANGE IN HARDENING
On hardening CNLHSS Steel 15-5 PH Stainless Steel, a dimensional change will take place. Typical dimensional changes are shown in Table 8. They can vary from heat to heat.
TABLE 8 – CONTRACTION FROM HEAT TREATMENT
Data represent single tests from one heat.
The general level of corrosion resistance of CNLHSS Steel 15-5 PH Stainless Steel exceeds that of Types 410 and 431, and is approximately equal to that of CNLHSS Steel 17-4 PH Stainless Steel.This is indicated by laboratory tests in both strongly oxidizing and reducing media, as well as by atmospheric exposures. In all heat-treated conditions, this alloy exhibits very little rusting after 500 hours exposure to 5% salt fog at 95 °F (35 °C).
When exposed to seacoast atmospheres for long periods of time,the material gradually develops a superficial layer of rust like other precipitation-hardening stainless steels. The general level of corrosion resistance is best in the fully hardened condition, and decreases slightly as the aging temperature is increased.
TABLE 9 - CORROSION RATES IN VARIOUS MEDIA
*Inches per month
**Inches per year.
TABLE 10 - STRESS CORROSION CRACKING TEST RESULTS OF CNLHSS STEEL 15-5 PH*
*NF indicates no failure.
(1) Cracked at code numbers that were stamped near the ends of specimens. Materials Performance Vol.26, No. 2 (1987).
TABLE 11 – 5% SALT FOG EXPOSURE FOR 10 DAYS
For all stock availability contact Sales.
On hardening CNLHSS Steel 15-5 PH Stainless Steel, a dimensional change will take place. Typical dimensional changes are shown in Table 8. They can vary from heat to heat.
TABLE 8 – CONTRACTION FROM HEAT TREATMENT
Condition | Contraction, in./in. (mm/mm) |
---|---|
H 900 | 0.00045 |
H 925 | 0.00051 |
H 1025 | 0.00053 |
H 1100 | 0.0009 |
H 1150 | 0.0022 |
H 1150-M | 1400 ––––> 0.00037 1150 ––––> 0.00206 1400 + 1150 ––––> 0.00243 |
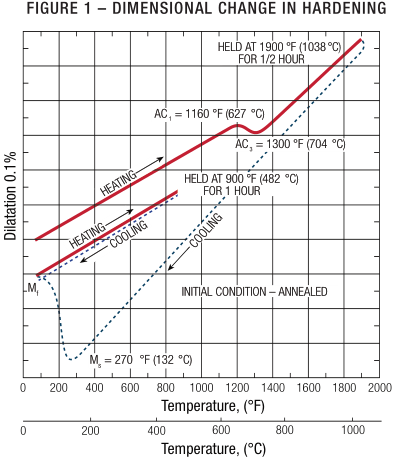
The general level of corrosion resistance of CNLHSS Steel 15-5 PH Stainless Steel exceeds that of Types 410 and 431, and is approximately equal to that of CNLHSS Steel 17-4 PH Stainless Steel.This is indicated by laboratory tests in both strongly oxidizing and reducing media, as well as by atmospheric exposures. In all heat-treated conditions, this alloy exhibits very little rusting after 500 hours exposure to 5% salt fog at 95 °F (35 °C).
When exposed to seacoast atmospheres for long periods of time,the material gradually develops a superficial layer of rust like other precipitation-hardening stainless steels. The general level of corrosion resistance is best in the fully hardened condition, and decreases slightly as the aging temperature is increased.
TABLE 9 - CORROSION RATES IN VARIOUS MEDIA
Corrosive Media | Time | Condition | Corrosion Rate |
---|---|---|---|
65% HNO3 | Average 5 - 48 hour periods | H 900 H 1025 H 1150 |
0.0083 IPM*(0.210 mm) 0.0106 IPM(0.269 mm) 0.0083 IPM(0.210 mm) |
1% HCI, 95 °F (35 °C) | Average 5 – 48 hour periods | H 900 H1025 H 1150 |
0.025 IPY**(0.635 mm) 0.085 IPY(2.159 mm) 0.730 IPY(18.542 mm) |
Commercial bleach 93 °F (35 °C) |
7 days | H 900 H1025 H 1150 |
0.0016 IPY(0.040 mm) 0.013 IPY(0.330 mm) 0.0083 IPY(0.211 mm) |
**Inches per year.
TABLE 10 - STRESS CORROSION CRACKING TEST RESULTS OF CNLHSS STEEL 15-5 PH*
Heat | Heat Treatment | 0.2% YS, ksi. (MPa) | Time to Failure, days under stress of | |
100% YS | 75% YS | |||
F | Condition A | 133 (917) | NF, NF, NF | NF, NF, NF |
E F |
H 900 | 180 (1241) 173 (1193) |
22, 22, 22 21, 21, 21 |
22, 22, 22 21, 21, 28 |
E F |
H 925 | 172 (1186) 166 (1145) |
22(1), 22(1), 266(1) 23(1), 23(1), 23(1) |
22(1), 22(1), 109(1) 23(1), 23(1), 23(1) |
E F |
H 975 | 163 (1124) 159 (1096) |
NF, NF, NF NF, NF, NF |
NF, NF, NF NF, NF, NF |
E | H 1025 | 159 (1096) | NF, NF, NF | NF, NF, NF |
(1) Cracked at code numbers that were stamped near the ends of specimens. Materials Performance Vol.26, No. 2 (1987).
TABLE 11 – 5% SALT FOG EXPOSURE FOR 10 DAYS
Condition | Rating |
H 900 | A+ (0% rust and stain covered) |
H 1025 | A (0 – 5% rust and stain covered) |
H 1150 | A (0 – 5% rust and stain covered) |
For all stock availability contact Sales.
Properties
FORMABILITY
Because CNLHSS Steel 15-5 PH Stainless Steel in Condition A is strong, forming normally should be limited to mild operations. However, fabrication can be improved greatly by heat treating before cold working. Table 12 indicates minimal bend radii for forming this material.
TABLE 12 – BEND TEST DATA MINIMAL BEND RADIUS*
Condition |
90° |
135° |
180° |
|||
---|---|---|---|---|---|---|
L |
T |
L |
T |
L |
T |
|
A |
3T |
4T |
3T |
5T |
6T |
9T |
H 900 |
3T |
4T |
3T |
6T |
5T |
9T |
H 925 |
2T |
4T |
3T |
6T |
5T |
9T |
H 1025 |
2T |
4T |
3T |
6T |
4T |
7T |
H 1075 |
2T |
4T |
3T |
4T |
4T |
7T |
H 1150 |
2T |
2T |
2T |
3T |
4T |
6T |
WELDABILITY
The precipitation hardening class of stainless steels is generally considered to be weldable by the common fusion and resistance techniques. Special consideration is required to achieve optimum mechanical properties by considering the best heat-treated conditions in which to weld and which heat treatments should follow welding. This particular alloy is generally considered to have equivalent weldability
to the most common alloy of this stainless class, CNLHSS Steel 17-4 PH Stainless Steel. When a weld filler is needed, AWS E/ER 630 is most often specified. CNLHSS
Steel 15-5 PH Stainless Steel is well known in reference literature and more information can be obtained in the following ways:
1.ANSI/AWS A5.9, A5.22, and A5.4 (stainless steel filler metals, welding electrode specifications)
HEAT TREATMENT
For maximum hardness and strength, material in the solution-treated condition is heated for one hour at 900 °F ± 15 °F (482 °C ± 8.4 °C) and air cooled to room temperature. If the material is purchased in the solution-treated condition (Condition A) and not subsequently hot worked, the hardening treatment can be performed without solution treating before hardening.
Where ductility in the hardened condition is of importance, better toughness can be obtained by raising the temperature of the hardening heat treatment. Unlike regular hardenable materials that require hardening plus a tempering or stress relieving treatment, this alloy can be hardened to the final desired properties in one operation. By varying the heat-treating procedure between 900 – 1150 °F (482 – 621 °C) for one to four hours, a wide range of properties can be attained.
If the alloy is not sufficiently ductile in any given hardened condition, it can be reheated at a higher hardening temperature to increase impact strength and elongation.
This can be accomplished without a solution treatment prior to final heat treatment. However, strength will be reduced.
For hot-worked or overaged material, a solution treatment at 1875 – 1925 °F (1024 – 1052 °C) for three minutes for each
0.1 in. (2.5 mm) of thickness, followed by cooling to at least
90 °F (32 °C) must be done prior to hardening. The solution treatment refines the grain size and makes hardened material more uniform.
When fabricating CNLHSS Steel 15-5 PH Stainless Steel, it is important to keep in mind the low temperatures at which the start of transformation to martensite (Ms) and the completion of the martensite transformation (Mf) occur. These temperatures are approximately 270 °F (132 °C) and 90 °F (32 °C) respectively.
Because of this characteristic, it is necessary to cool parts in process at least to 90 °F (32 °C) prior to applying subsequent heat treatments if normal final properties are to be obtained. This practice is essential to assure grain refinement and to assure good ductility.
Descaling
Hardening treatments produce only a light heat tint on surfaces. This tint can be removed easily by mechanical means such as wet grit blasting or with a short pickle in 10% nitric – 2% hydrofluoric acid (by volume) at 110 – 140 °F (43 – 60 °C). Where pickling is undesirable, heat tint may be removed by a light electropolishing operation. The latter two treatments also clean and passivate the surfaces for maximum corrosion resistance.Where solution treating is performed, the following pickling method satisfactorily removes surface scale. The use of molten salts such as sodium hydride or Kolene processes to descale is limited since these methods partially harden solution-treated material.
In pickling operations, time and temperature should be controlled closely to obtain uniform scale removal without over etching. Scale softening methods may be used on material that has been solution treated (not pickled) and precipitation hardened.
TABLE 13
Procedure |
Acid Bath |
Temperature, °F (°C) |
Time at Temperature Minutes |
Rinse |
---|---|---|---|---|
Step 1 |
Caustic Permanganate |
160 – 180 (71 – 82) |
60 |
Water |
Step 2 |
10% Nitric Acid + 2% Hydrofluoric Acid |
110 – 140 (43 – 60) |
2 – 3 |
Hot water, high pressure water or brush scrub |
For all stock availability contact Sales.